Plastics recycling
Our solutions
• Dissolution
• Depolymerization
• Conversion
Back in the 1990s, with the increasingly widespread use of PET as a food packaging material, IFPEN launched its first research projects focusing on recycling via depolymerization. But mechanical recycling technologies were sufficient at the time to meet the sector’s needs.
In 2013, following the emergence of new challenges associated with the circular economy in France and throughout Europe, IFPEN once again turned its attention to plastics recycling. Addressing the limitations of mechanical recycling and the sector's expectations, its teams drew on long-standing expertise to examine and develop new solutions:
Our chemicals and process development expertise enables us to credibly position ourselves in the advanced recycling sector, which offers real development potential, as a complement to mechanical recycling, for specific types of plastic.
Alexandra Chaumonnot, PVC Recycling project manager, IFPEN
The different solutions examined by IFPEN cover all three possible loops associated with advanced recycling. They are chosen on the basis of the nature, quality and quantity of the plastics flows to be processed – highly dependent on the collection and sorting channels in place – with a view to reintroducing the products obtained following conversion at the most appropriate stage in the process to obtain plastic materials.
One of the keys to ensuring these solutions come to fruition is to establish partnerships with players in the sectors concerned, particularly with a view to accessing the demonstration and industrial development phases as quickly as possible, in order to pave the way for the marketing of these new technologies.
Following several validation steps, a recycling process via depolymerization consisting in breaking down the plastic waste into base monomers, is currently being demonstrated on an industrial scale with a view to its market launch. Conclusive research that IFPEN’s teams now want to extend to different processes related to other chemical recycling loops. For example, dissolution offers a shorter recycling circuit, since it extracts all the additives in order to obtain a purified polymer.
Conversion on the other hand, involves a longer recycling circuit, since waste plastics are first broken down into a liquid or gas raw material (hydrocarbon cuts) that is then reintegrated further upstream in the production chain (at the refinery or petrochemicals complex) before being used for the production of fuels or chemical products, including plastics.
The set of solutions being considered covers two complementary strategic avenues. Dissolution and depolymerization are aimed at obtaining products (polymers and monomers) with high added value on the basis of short loops (favorable in terms of LCA). This involves processing specific plastic waste (carefully sorted flows) and developing ad hoc technologies. Furthermore, although it is a longer process, conversion makes it possible to process plastic blends (and complex plastics), significant in terms of quantity and compatible with tried and tested refining/petrochemical processes.
PURIFICATION OF POLYMERS VIA THE DISSOLUTION OF PLASTICS
Our research relates to plastics recycling using dissolution: dissolution via the addition of a solvent makes it possible to isolate and purify the polymer without depolymerizing, which is useful, particularly in terms of LCA optimization.
Alexandra Chaumonnot, PVC Recycling project manager, IFPEN
Depolymerization of PET
What is PET used for? What challenges for its recycling?
Polyethylene terephthalate - or PET - is usually produced from fossil matter, via the synthesis of an acid that, when combined with an alcohol, results in a monomer. The polymer produced is used for the manufacture of colorless, clear bottles for mineral water and fizzy drinks. PET is also increasingly used as an ingredient in opaque containers, such as milk bottles, cosmetics packaging and household products.
Globally, PET amounts to around 90 million metric tons per year (Mty): 30% for packaging and 70% for textiles.
In Europe, the consumption of PET resins for packaging production represented just over 4 Mt in 2018.
Today, closed-loop mechanical recycling – i.e., used, once again, to produce recyclable containers for the same applications - is a satisfactory solution for colorless clear PET bottles. Conversely, colored clear PET, which tends to be sorted together with opaque PET, cannot be returned to its original application. At best, colored or opaque PET undergoes open-loop recycling for other usages, such as technical fibers, nonwoven fabrics or strapping.
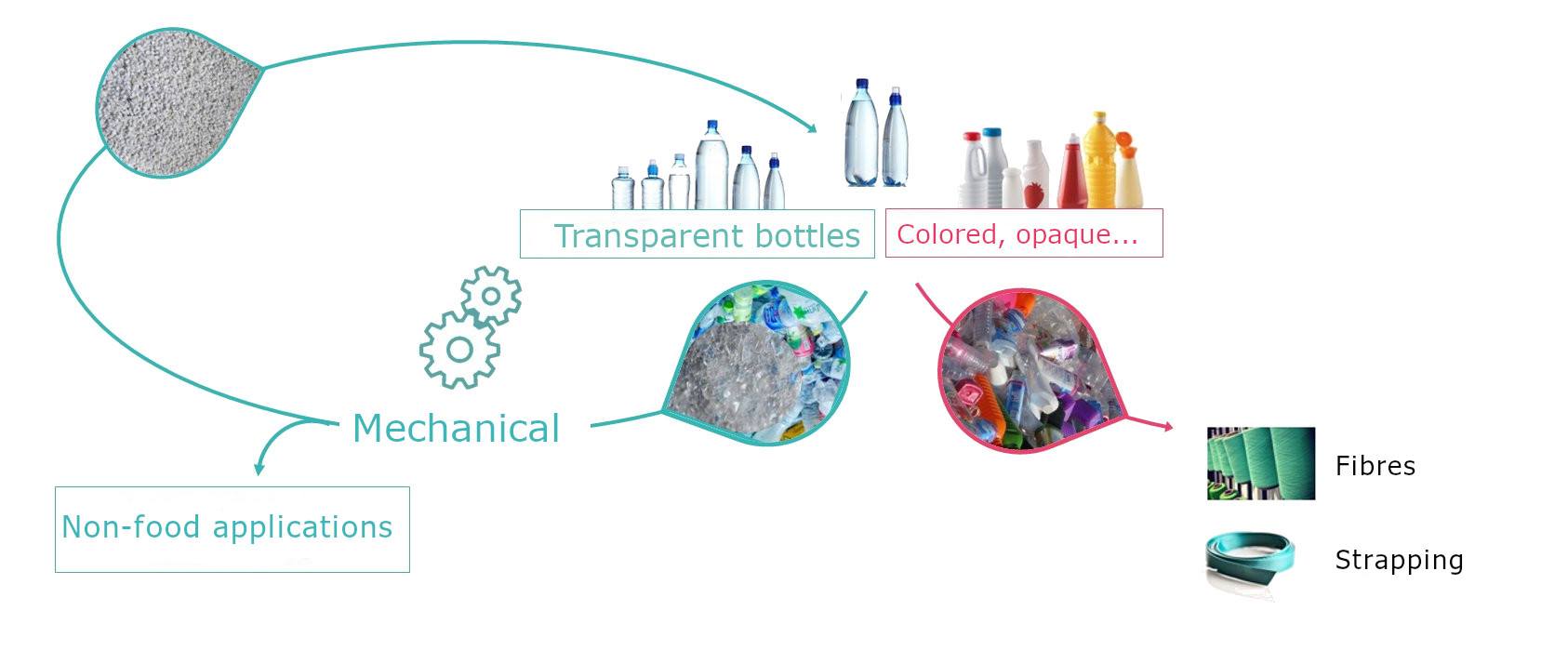
It is estimated that just 1 in 10 rigid PET packaging containers is turned back into a rigid container following mechanical recycling.
Since it makes it possible to close the loop following collection of colored and opaque packaging, a chemical recycling technology serves as a useful complement to mechanical processes, overcoming their limitations.
In this context, IFPEN has developed a glycolytic depolymerization, depigmentation and decolorization process: Rewind™ PET.
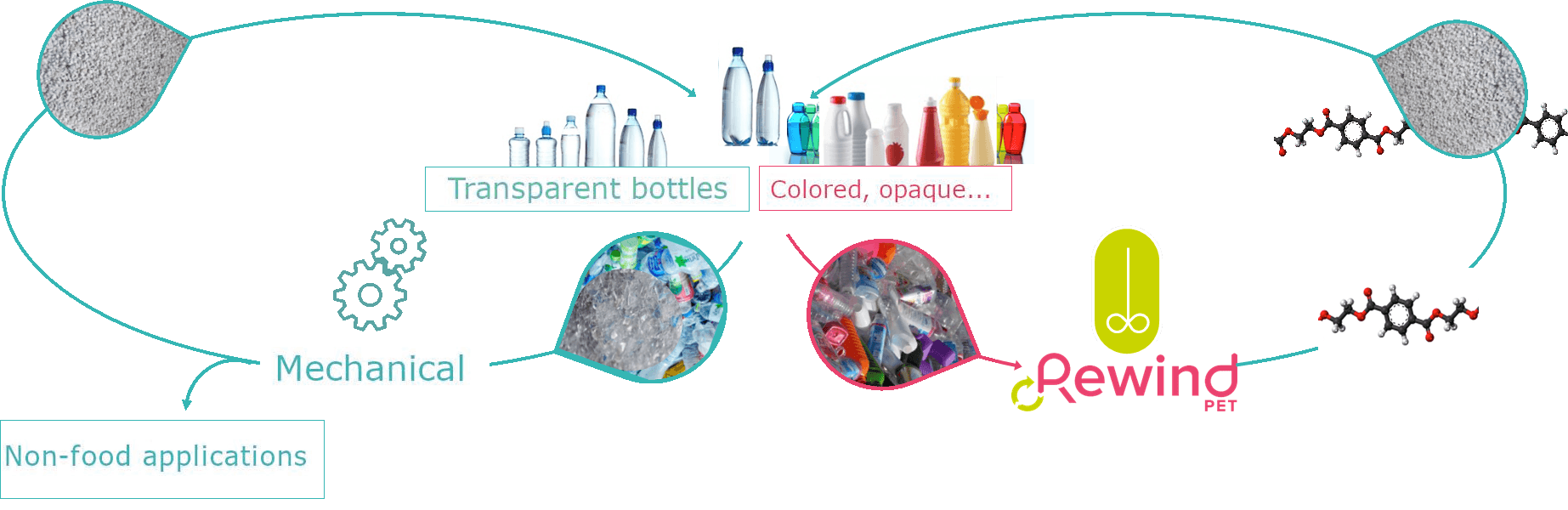
The project, launched in 2015, went through each of the validation steps prior to industrial scale-up, drawing on tried and tested technologies and IFPEN’s specific expertise:
• in the laboratory: proof of concept for the key elements in the process;
• on an intermediate scale: study of yields and the quality of the product obtained in optimized operating conditions, from several tens of kilos of PET flakes collected in French regeneration plants with high concentrations of opaque PET;
• at each step: identification of compounds present and mechanisms at play;
• with, ultimately, the evaluation of the economic viability of the process.
Frédéric Favre, PET recycling process project manager, IFPEN
The Rewind™ PET process will make it possible to recycle all PET waste. Initially, it consists in depolymerizing colored and opaque PET flakes. This operation produces a medium comprising a mixture of the monomer with its pigments and dyes. The monomer obtained is then purified, i.e., its pigments and dyes are removed.
The principal challenge, purification, lies in isolating the monomer with an adequate degree of purity from the dyes and pigments. This condition must be met in order for the monomer to be reused in a PET plant to produce all types of PET, including for food applications.
The Rewind™ PET process in video (French version)
What is the technological maturity of the Rewind™ PET process?
Today, the focus is on validation of the industrial scale-up of the entire process. To this end, IFPEN, Axens and Jeplan - a Japanese company also involved in recycling via depolymerization - have pooled their operational, engineering and technological expertise.
In 2020, the partners signed a development and marketing agreement aimed at developing, demonstrating and marketing this innovative process. They are targeting the exclusive marketing by Axens of the Rewind™ PET process globally by the end of 2022.
CONVERSION OF PLASTICS TO OIL CUTS
Conversion involves the thermal or thermocatalytic cracking of plastics. Unlike depolymerization, this method makes it possible, upstream of the monomer, to return to hydrocarbon cuts that are subsequently subject to industrial refining and petrochemical processes (steam cracking, for example). These chemical intermediates can then be used instead of raw materials of fossil origin to manufacture monomers and thereafter polymers.
We are studying the conversion of plastics via catalytic pyrolysis, which consists in purifying pyrolysis oils in order to be able to reuse them in a traditional refining process.
Wilfried Weiss, Recycling process project manager, IFPEN