Electrified Mobility
OUR solutions
The solutions proposed by IFPEN concern:
- Eco-designed electric machines for mobility, with very high efficiency and high performance densities
- Innovative motor topologies such as the axial flux machine or the Pure Synchro-Reluctante topology (without magnets)
- New generations of power electronics optimized for wide gap transistors: SiC, GaN.
- New concepts of high-efficiency active (liquid heat transfer injection, immersion) or passive (potting, conduction components, etc.) cooling systems at reduced cost for both electrical machines and future generation electronics.
- Advanced control of electrical systems, based on optimal, robust and easily deployed approaches.
- The holistic approach to compromises for optimizing the performance of electrical systems: power, efficiency, ecological impact, cost, noise, etc.
These innovative solutions can be developed for all mobility markets, whether for large-scale automobile series, the off-road market or light and gentle mobility.
Development of synchronous reluctance electric machines
IFPEN is developing a set of technological building blocks allowing the system developed to meet the wide variety of specifications targeted by mobility. These bricks concern both the motor, focusing in particular on its active parts (rotor, stator and winding), the power electronics, the cooling system allowing the whole to be compacted, as well as the mechanical and mechatronic integration at a constrained volume. and minimizing the impact on the product life cycle. These technologies are developed within the framework of collaborative projects conducted both within the French and European research ecosystems with many major public and private players, as well as with SMEs and start-ups for short and medium production runs.
Among all the existing electric motor technologies, IFPEN has focused its development on the synchro-reluctant motor assisted by magnets with or without rare earths. The latter has a quadruple advantage:
• by exploiting the reluctance phenomenon, it uses fewer magnets than permanent magnet synchronous motors,
• this characteristic gives it an advantage in terms of production cost and environmental impact,
• it offers a wide range of high efficiency compared to motors on the market, allowing it to optimize the use of energy and reduce the size of the vehicle battery,
• and this topology is conducive to efficient operation at high speed, which gives it an advantage of power densification and reduction of the size of the propulsion system
Based on this technology, IFPEN has developed three power ranges, aimed at either short production runs, or IC vehicle retrofit applications:
• less than 60 V / 40 kW
• between 60 V / 40 kW and 350 V / 150 kW
• between 350 V / 150 kW and 800 V / 300+ kW
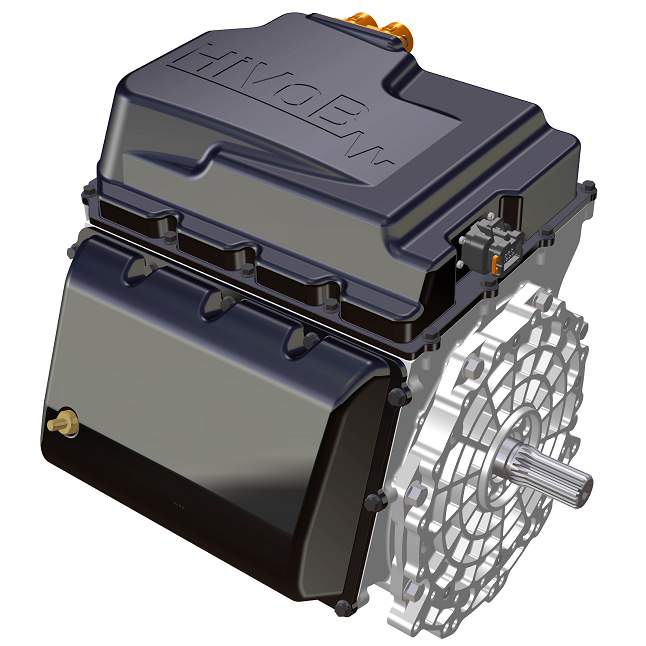
An efficient technology: electric synchronous reluctance motors
IFPEN’s teams decided to develop synchronous reluctance electric powertrain technology to meet two major objectives:
• develop a highly efficient, modular and robust motor able to cope with extreme operating conditions;
• identify the most attractive performance / cost / manufacturability compromise for small series markets. As this approach requires more advanced and complex engine torque management to compensate for the small number of magnets, IFPEN developed highly efficient adapted control laws.
The efficiency of a synchronous reluctance motor is highly dependent on the design of the active components (rotor, stator). It is for this reason that IFPEN has developed design tools based on system optimality and a proprietary technology for these active components in order to optimize their performance with respect to the state of the art while minimizing costs.
Electric machines that contain few rare earths and are highly recyclable
The rare earths used in the magnets of the active components of electric motors are critical materials. It is important to minimize their use and recycle them. Two principal strategies are deployed to achieve this objective. Firstly, IFPEN’s design tools make it possible to optimize the design of the active components - particularly the rotor - in order to reduce the amount of magnets, and hence of rare earths. In particular, for some applications, a systems engineering approach even makes it possible to get rid of them, in particular by using magnets based on ferrites of non-prismatic shapes: this is possible by optimizing the powertrain as a whole, integrating the electric motor first but also the electronics of power and the single or two-speed reducer.
In parallel, design work is being carried out to facilitate the end-of-life collection of strategic materials, Innovative technologies for the manufacture of permanent magnets are being used to save raw materials. One example is the use of powder injection molding (PIM) .
Efficient electric powertrains and material savings
IFPEN is designing efficient electric powertrains, incorporating compact electronics and an original engine cooling solution. These technologies cover a broad range of applications, from the small low-voltage vehicle to vehicles requiring high powers.
In addition, these motors are designed with a view to recycling and reducing the quantity of material used. For example, the MELCHIOR project, conducted by the IFPEN Transports Energie and CEA Energies du Futur Carnot Institutes from 2022 to 2023, consisted in designing and developing a synchronous reluctance motor whose active components require a smaller number of magnets for a given power (125 kW/kg of magnet, i.e., + 40% compared to the state of the art). The magnets can also be collected at the end of the life cycle, thereby reducing the amount of materials lost and helping to meet the needs of the recycling sector. The Melchior project has been followed up by the European Magellan project, bringing together the two Carnot Institutes and the industrial partner Orano with the aim of making further progress in the production of European permanent magnets and in the recycling of critical materials essential to the manufacture of electric motors.
Close links with the SME community
IFPEN joins forces with SMEs for the design and manufacture of motors.
For example, a partnership has been forged with SME Solution F (GCK Group) to develop new generations of compact, ultra-high specific power electric powertrains to equip different vehicle categories, including racing models, passenger cars, trucks and off-road vehicles. Vincent Lallemand, Director of Solution F, explains: “First of all, we adapted IFPEN’s magnet-assisted synchronous reluctance motor technology as part of the electric retrofit of the Lancia Delta HF Integrale classic car. This technology was then extended to ultra-high-voltage (800 V) powertrains for snow groomers, and low-voltage (48 V) powertrains for leisure vehicles and retrofit hybridization of light urban cars. This technology sets us apart and is strategic for our group. It gives us a head start in electric powertrain technologies designed either for retrofitting IC vehicles, or for the small-scale production of high-performance, premium electric cars.”
Another partnership was initiated in 2023 with MOV’NTEC (based in the Hauts-de-France region of northern France) to develop and industrialize a range of electric motors optimized in terms of efficiency, volume and mass and with a low environmental footprint (local supply, zero waste in manufacturing, repairable during their life and recyclable at the end of their life).
The design of an innovative architecture: axial flux machine
In the field of electrical machines, IFPEN is exploring technological avenues other than the synchro-reluctant machine, with a view to significantly improving the torque density.
As part of the ANR RedHat project, coordinated by the LSEE laboratory, teams from IFPEN and its partners have designed a high-performance axial flux motor developed on the basis of a double stator/single rotor topology. The purpose of this project is to maximize machine performance, by incorporating several innovations in terms of stator and rotor thermal management. To this end, the project uses new materials including inorganic insulators for the windings; these are capable of withstanding, in steady state, much higher temperatures than those tolerated by standard organic polymer insulators. IFPEN provided advanced 3D models, combined with optimization tools, for the dimensioning of the magnetic circuits and the estimation of the distribution of thermal and mechanical stresses within the motor. It also introduced models to validate the degree of mechanical deformation of the rotor under the effect of electromagnetic forces, as well as the efficiency of the stator and rotor cooling system.
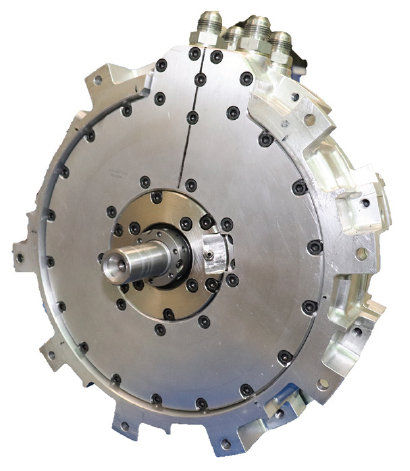
New generations of power electronics
IFPEN is developing power electronic converters that carry out several functions: electric motor management, onboard vehicle energy management and battery recharging control. Open, robust and versatile, they support engine development and control.
These electric energy converters uses transistors made from WBG (Wide Band Gap) materials such as silicon carbide (SiC) and gallium nitride (GaN)
The technological breakthrough introduced by WBG components goes hand in hand with some major challenges now being addressed by IFPEN:
1) Understanding and characterizing WBG (Wide Band Gap) components within an electric system
Power topologies play a critical role in improving the sustainability of power systems, optimizing energy efficiency and extending component life. IFPEN offers innovative architectures to efficiently exploit WBG components, while increasing the mass and volume power densities of converters
To better understand the impact of these new technologies and their aging mechanisms that can reduce the performance of electric converters, IFPEN is participating in a number of European projects (i.e. ARCHIMEDES) and has forged specific partnerships. For example, in 2023, IFPEN joined forces with Cambridge GaN Devices (CGD), a company specializing in semi-conductors proposing a range of highly energy-efficient WBG GaN components, with a view to developing an innovative inverter for electric mobility using advanced GaN solutions.
2) New topologies
Power topologies play a critical role in improving the sustainability of power systems, optimizing energy efficiency and extending component life. IFPEN offers innovative architectures to efficiently exploit WBG components, while increasing the mass and volume power densities of converters: in this context, IFPEN is participating in the European EMPOWER project, in which a very high power density inverter is being developed for heavy-duty applications.
3) Thermal management and new cooling solutions
Using WBG components to their full potential can generate local power losses in the order of 1 kW/cm2, i.e., ten times greater than those of Si chips. IFPEN explores new localized cooling solutions for the semiconductor chip, focusing particularly on a better understanding of the thermal behavior of the components incorporated in circuit boards.
Power electronic converters incorporating WBG components
Using WBG components, IFPEN is working with its partners to develop power electronic converters adapted to different usages. For example, two inverters based on SiC components have been developed: HivoSic, a polyvalent three-phase 800 V SiC inverter for test bench applications, and TwinSic, an ultra-high-power SiC inverter for electric vehicles. half-bridge power module based on ICeGaN components from CGD has also been developed. It constitutes the elementary building block of a new generation traction inverter in GaN technology.
![]() |
![]()
|
![]()
|
Close links with SMEs to develop and disseminate new technologies
IFPEN joins forces with SMEs for the design, manufacture and marketing of power electronics for electric motors. The search for partners is facilitated by industry associations such as the CARA cluster, which brings together 430 manufacturers, transport operators and research and training centers in the Auvergne Rhône Alpes region of southern France.
One such partnership is with Lyon-based company Alphée Développement to market the ultra-high-power HivoSiC inverter.
In addition, IFPEN, within the framework of its partnership with the SME Solution F (from GCK Group) relating to the development of a low-voltage (48V) synchronous reluctance motor for leisure vehicles and the retrofit hybridization of light urban cars, has granted Solution F an operating license for an inverter of a low voltage inverter very innovative in terms of continuous powerthat ensures optimal control of this motor.
Compact inverter for fuel cell compressor control
IFPEN has developed compact, modular power and voltage electronics (8 and 30 kW) and associated control algorithms to operate a new generation of air supply compressors for hydrogen fuel cells (PEMFC). This modularity was offered by an innovative design and integration of SiC components in a discrete package, making this technology economically viable for this range of applications.
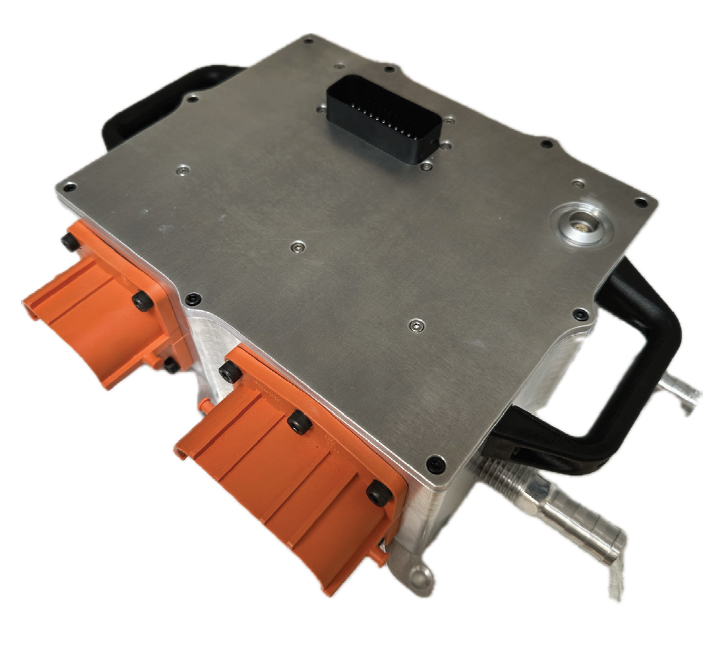
Electric machine management
IFPEN develops advanced control strategies dedicated to electric machine management. These control strategies or laws are designed and validated in a specific proprietary development environment (eDrive Control Suite) that automatically generates the code to be integrated in the control electronics (inverters). This environment makes it possible to design and calibrate the algorithms necessary for the precise management of electric machines operating at high speed, characterized by a high electric frequency. The adaptation of the control software to each targeted application follows a process honed over several years, relying on simulation or experimental characterization. The software solutions developed in just a few days are embedded in a control card, integrated into all inverters developed and produced by IFPEN’s teams. The combination of high-performance algorithms quickly deployed with compact electronic systems characterized by small losses makes it possible to fully exploit the potential of the new-generation electric machines designed by IFPEN and its industrial partners.
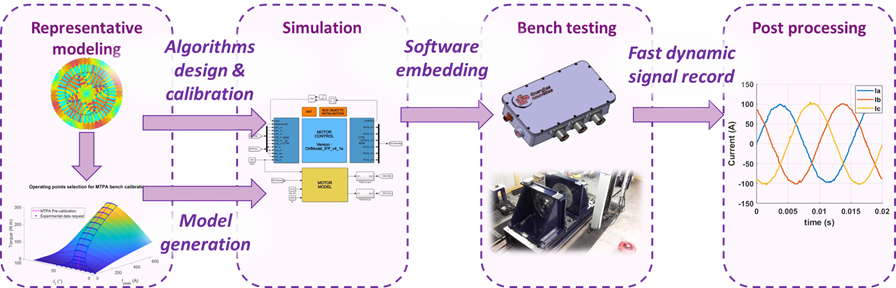
The strategies developed allow operation at optimal efficiency in all conditions, optimize noise by injecting destructive interference vibrations, optimize the compromise between motor and inverter losses, etc.
These advanced control strategies have been tested within the framework of several collaborative projects, including the CORAM Olea-Evo project conducted by Silicon Mobility, an SME specializing in semiconductors and onboard software. Work is being carried out aimed at increasing the range of electric vehicles by reducing losses in the inverter and the electric motor through the implementation of innovative control algorithms. IFPEN’s teams have developed advanced models to estimate these losses and thus enable their optimization through control. The CORAM Mautiv’8 project, carried out with Punch Powertrain France, a manufacturer of mass-produced power electronics, focuses on the reduction through control of electrical disturbances linked to the use of SiC transistors. Finally, IFPEN also collaborates directly with tier 1 equipment suppliers and automobile manufacturers to assess the relevance of its innovative control solutions.
Innovations to support light and soft mobility
IFPEN is supporting the expansion of light mobility, and electric bikes in particular, by creating digital services and proposing innovative technical solutions.
For example, IFPEN has developed discharge prediction algorithms to help cyclists manage the battery efficiently.
IFPEN also designs automatic transmission systems for electric bikes and light quadricycles. For example, the innovative transmission concept for electric bikes, which automatically adapts the gear engaged and eliminates the derailleur and sprocket cassette, is currently being developed.
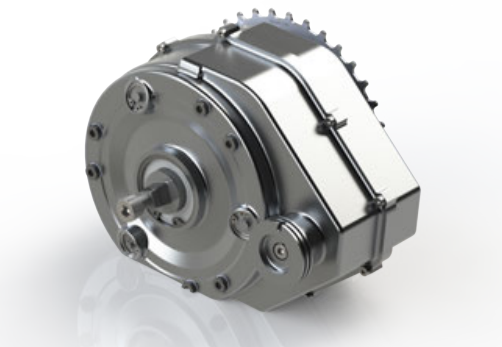