Testimony of Li Zhang, process engineer at IFPEN
According to the NZE (Net Zero Emission) scenario of the IEAa, the deployment of CCUS (Carbon Capture, Utilization and Storage) needs to accelerate and increase from around 40 Mt of CO2 captured globally in 2022 to 1 Gt in 2030 [1]. Among the solutions developed, post-combustion capture using solvents is, so far, considered to be one of the most robust, efficient and appropriate [2].
The DMXTM solution, which addresses the need to have access to effective and economical technologies, is one such option. The fruit of more than 10 years research at IFPEN, this technology, now entering the final development phase, had to be demonstrated in a real industrial setting [3] [4].
Hence the launch of the 3Db (DMX Demonstration in Dunkirk) project in 2019 to build an industrial demonstrator. And where better to build it than at one of Europe’s biggest industrial sites, thereby contributing to the decarbonization roadmap of one of France’s leading emitters, the ArcelorMittal’s steelworks in Dunkirk (Image 1)?
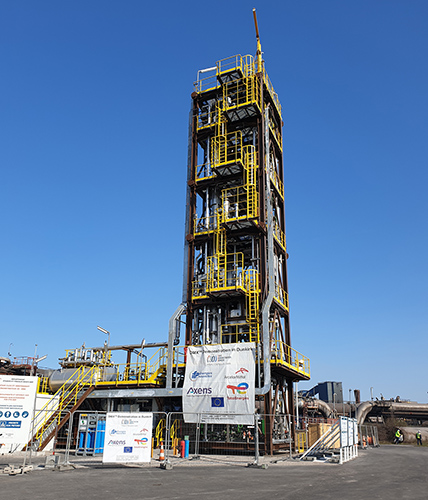
This project required input from a dedicated IFPEN team based at the industrial site, to monitor the construction and conduct tests, with remote support from the IFPEN team at the Solaize site. For the very first time, IFPEN was responsible for an operation on an outside industrial site!
Modules more than 26 meters in height arrived at the site in November 2021, following months of workshop studies and construction.
Once the demonstrator had been connected to the steelworks site’s blast furnace gas pipes, unit start-up operations began in March 2022 with technical coordination provided by partner AXENS (Image 2).
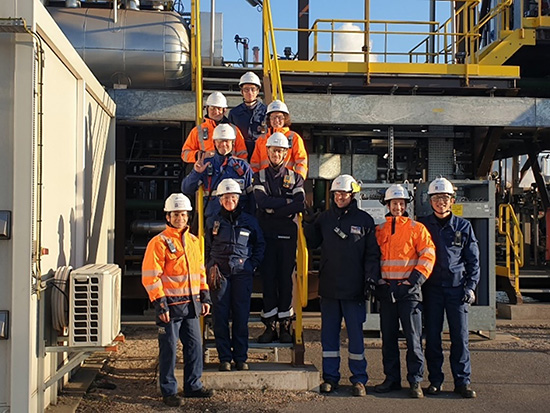
In my capacity as a process engineer at IFPEN, I monitored the tests from their launch through to the end of the test campaign at the Dunkirk site. Before going there, I had worked as a process design engineer, using an early version of the numerical DMXTM simulator. This time, I found myself “on the other side”, contributing to the acquisition of experimental data used to improve the simulation model, which will be used for sizing future equipment!
I was also exposed to the reality on the ground and the unexpected events that can occur during a demonstration, occurrences that make each experimental aspect unique and invaluable. Industrial demonstration and process design are two sides of the same coin in this respect!
Now, just over two years after the completion of on-site construction, the demonstration of the DMXTM process has ended. After evaluation of the composition of the gases representative of different applicationsc (steelworks, cement works or electric power plant), the performances of the capture process have been validated, highlighting various benefits:
- a significant reduction in energy penalty (30% lower compared to MEA or CESAR1d solvents),
- the solvent’s considerable capture capacity, high quality of the CO2 capturede,
- good solvent stability, etc.
In addition to the success of the demonstration, the data obtained during the test campaign formed the foundation to produce a new version of the simulator that partner AXENSf will benefit from.
Although the demonstration phase for the DMXTM process has now been completed, the Dunkirk facility is going to be used for a further few months to test a new solvent formulation. This time, I will follow the tests from my base at IFPEN but it will be an opportunity for other colleagues to go and be part of this unique experience: to see the culmination of years of research supporting the decarbonization of industry and thereby help to combat climate change.
a- International Energy Agency.
b- Project partners: ArcelorMittal France, TotalEnergies and AXENS. Demonstrator capacity: 0.5t CO2 captured per hour.
c- Blast furnace gas was used as the unit’s base feedstock gas, but other compositions were deliberately produced via the unit’s recycling operations, in order to validate the DMXTM process for different applications.
d- MEA: aqueous solution with monoethanolamine, CESAR1: aqueous solution with aminomethyl propanol (AMP) and piperazine (PZ).
e- Purity of CO2 above 99% (dry CO2).
f- Software development led by P. Bachaud and V. Carlier.
References:
-
IEA Ed.
>> https://www.iea.org/reports/world-energy-outlook-2023
-
L. Raynal, P.A. Bouillon, A. Gomez, P. Broutin, From MEA to demixing solvents and future steps, a roadmap for lowering the cost of post-combustion carbon capture, Chemical Engineering Journal 171 (2011) 742-752.
>> DOI: 10.1016/j.cej.2011.01.008
-
P. Broutin, P. Briot, S. Ehlers, A. Kather, Benchmarking of the DMXTM CO2 Capture Process, Energy Procedia 114 (2017) 2561-2572.
>> DOI: 10.1016/j.egypro.2017.03.1414
-
M. Dreillard, P. Broutin, P. Briot, T. Huard, A. Lettat, Application of the DMXTM CO2 Capture Process in Steel Industry, Energy Procedia 114 (2017) 2573 -2589.
>> DOI: 10.1016/j.egypro.2017.03.1415
Scientific contact: catherine.laroche@ifpen.fr Project manager: Vania Moreau