Thesis prepared by Flavia Domingues de Souza: « Étude et modélisation d’une Machine à Mémoire de Flux Variable à base des aimants Fe-Cr-Co pour son alimentation et sa commande sans capteur mécanique à haute vitesse. » ("Study and modeling of a Variable Flux Memory Motor fitted with Fe-Cr-Co magnets for its power supply and sensorless high-speed mechanical control").
Permanent magnet synchronous motors (PMSM) are a reference technology for electric vehicle propulsion. However, their large-scale deployment is subject to the constraints associated with magnets:
- the capacity to obtain resources (particularly rare earths), since 40% of the raw materials required for their production are located in China;
- as well as the environmental challenges related to mining, recycling and refining.
In addition, PMSMs often require flux-weakening1 strategies in order to operate at high speeds, which can result in energy losses and, consequently, a reduction in the efficiency of the overall system.
Variable Flux Memory Motors (VFMM) represent an alternative technology that uses Fe-Cr-Co-based “reduced coercive field” magnets. Still little used for these applications, this alloy is advantageous due to its low cobalt content (critical metal) and its good mechanical resistance. Moreover, the control of VFMMs presents an additional degree of freedom since their magnetic flows can be regulated via very short pulses of magnetizing current.
The research conducted for this thesis was aimed at characterizing and understanding the behavior of the Fe-Cr-Co in the target operating conditions. To do so, the configuration studied was that of a PMSM, where the permanent magnet rotor was replaced by a solid cylinder of this alloy, a simple geometry and adapted to high-speed applications. The experimental study was conducted in two stages:
- standstill magnetization, via injection of currents in the stator windings at zero speed, with the aim of characterizing the magnet inserted into the machine environment;
- dynamic magnetization (rotating motor) in which the magnetization state is adjusted as the electric motor is driven, and which is used to control its electromagnetic torque.
The first step was based on equations describing operating points in the hysteresis loop and relating the magnetic field strength H to the magnetic flow density B [1]. Two methodologies were proposed and deployed to describe the magnetization profile of the Fe-Cr-Co at a standstill, as a function of being located either in the easy or difficult magnetization axis. The magnetic characteristics of the cylinder were deduced from standstill tests, as well as from finite element simulations and the results were compared to the references provided by ideal measurement equipment (Hysteresis Graph), which characterizes the magnet outside the machine environment. Figure 1 presents the differences observed, discussed in [2], for which the studies conducted via numerical simulation led to the conclusion that they are linked to the geometry and saturation of the material making up the stator.
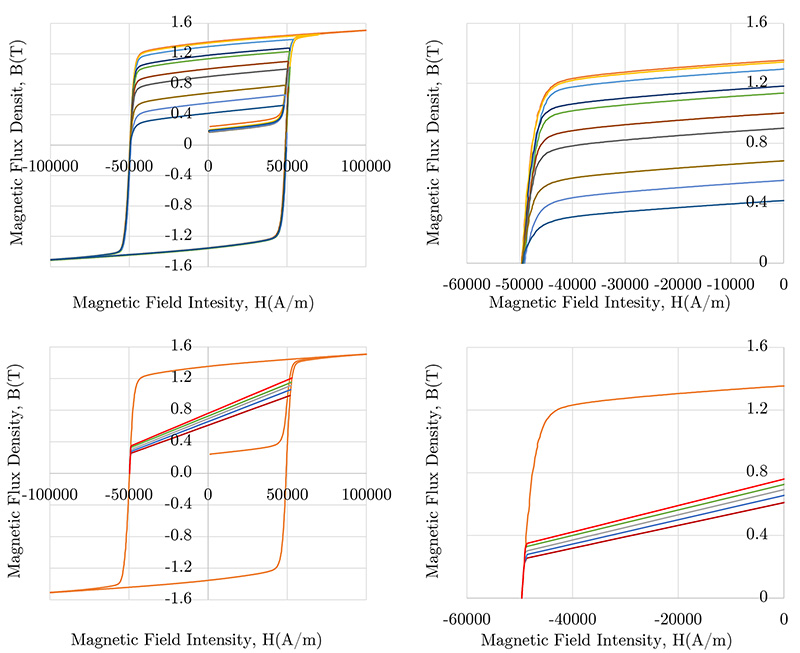
Line 1 graphs: from hysteresis graph measurements
Line 2 graphs: from experimental tests and finite element simulations
The second part, focusing on the dynamic magnetization and control of the motor’s electromagnetic torque, resulted in the development of a command algorithm without a rotor position sensor, adapted from previous research [3]. This system estimates the position and speed of the rotor using the measured output voltages, taking into account phase delay compensation. These are strongly influenced by the inductances of the direct and quadrature axes (dq axes)². A methodology using FEA simulations was proposed to estimate them, and also considering the anisotropic effects of the magnet and stator iron saturation.
An important result of this work relates to the partial magnetization states of the magnet, which were derived from the standstill magnetization tests, and were then used to predict the expected dynamic operating points. The magnet’s magnetic model resulting from the tests was also used as a basis for the analysis of machine inductances, information that is required to optimize the control of the system aimed at maximizing the torque generated by the machine.
Another conclusion concerns the demonstration of the influence of electric machine geometry (slot design, magnet length, etc.) on the magnetization state expected by a magnet inserted in an VFMM.
This research paves the way for further scientific studies aimed at improving the geometric design of a stator adapted and optimized for Fe-Cr-Co magnet properties.
1- Flux weakening of an operating machine consists in reducing the inductor flux in order to increase its speed beyond its nominal value without increasing the supply voltage.
2- Axes associated with changing the machine's real three-phase frame of reference to a rotating frame of reference fixed to the rotor, in order to align the model of an AC machine with that of a DC machine, allowing independent control of the flux and torque in the machine (vector command).
References
-
F. D. de Sousa, A. Battiston, S. Pierfederici and F. Meibody-Tabar, Validation of the standstill magnetization strategy of a FeCrCo-based Variable Flux Memory Machine, 2021 24th International Conference on Electrical Machines and Systems (ICEMS), Gyeongju, Korea, Republic of, 2021, pp. 536-541.
>> doi: 10.23919/ICEMS52562.2021.9634323
-
F. D. de Sousa, A. Battiston, F. Meibody-Tabar and S. Pierfederici, Evaluation of the Magnetic Behavior of a Single Pole Pair Fe-Cr-Co-based Memory Motor Considering a Standstill Magnetization, in IEEE Transactions on Magnetics, vol. 58, no. 8, pp. 1-7, Aug. 2022, Art no. 8202607.
>> doi: 10.1109/TMAG.2022.3141895
-
N. Haje Obeid and A. Battiston, Model based angle compensation method for sensorless control of a wide range high speed PMSM, IECON 2019 - 45th Annual Conference of the IEEE Industrial Electronics Society, Lisbon, Portugal, 2019, pp. 2701-2706.
>> doi: 10.1109/IECON.2019.8926751
Scientific contact: alexandre.battiston@ifpen.fr