In the energy and chemicals sectors, the conversion of raw materials into finished or semi-finished products is conducted via a succession of processes in dedicated units. Each of these processes comprises input conversion steps and output separation steps (Figure 1).
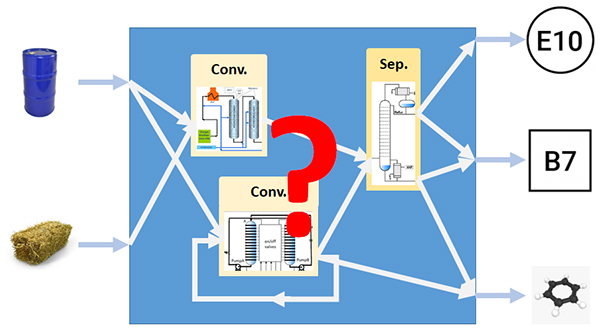
In an industrial context where the focus is on optimizing the use of resources and reducing the environmental footprint, the capacity to redefine and optimize the arrangement of units appeared essential at IFPEN. So its teams developed a tool for the purpose.
In the literature, the first mathematical approaches to the subject emerged at the end of the 1970s. They consisted in choosing the individual conversion and separation steps to be implemented, along with the routing of flows between feeds, individual steps and products. The most efficient solutions to emerge are based on MINLP (Mixed Integer Non Linear Programming) solvers enabling the use of both continuous and Boolean variables. The latter are required in terms of the mathematical formulation to manage the notion of unit and flow existence [1].
Despite research conducted to improve these solvers as well as problem formulation, tackling real industrial cases with existing MINLP solvers remains complex. The difficulty lies not only in calculation times but also in the capacity of the solvers to find solutions.
The need to take into account multiple variables - representing products, energy consumption and costs - led us to adopt a linear approach making it possible to use solvers that are far more efficient and robust. In this case, each individual step needs to be described by a meta-modela [2]. As well as obtaining representative linear meta-models, we developed a generic platform - FOX-Prod - enabling the deployment of the calculation tool and the maintenance of a database of meta-models of individual steps. The database used is the result of several years of capitalization in the refining and petrochemicals sectors. The platform is interfaced with GAMS software for algebraic modeling and optimization.
Initially, this platform was tested for a reduced, well controlled perimeterb after years of process development [3]. Thereafter, it successfully generated innovative unit configurations for a mature domain where the optimization margin was low. With meta-models obtained by learning from experimental design data, it was possible to propose the recycling of some flows and the pooling of separation steps.
The platform also enables optimization under constraints. Hence, Figure 2 represents differences for a reference industrial case with, firstly, the absolute optimum scenario and, secondly, an optimized scenario taking into account flow circulation constraints (“cfg retained”). The calculated gain, amounting to several tens of dollars per ton of feed processed and representing a substantial improvement (several percentage points), was then validated by simulations of the identified architecture.
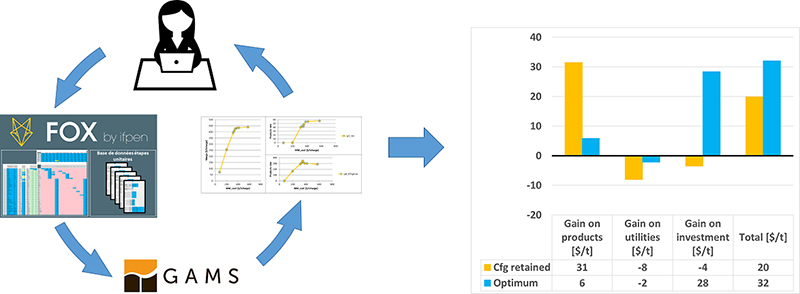
Subsequent research is aimed at extending the platform’s scope of application, particularly for plastics recycling and the production of a bio-based substance, and the meta-model database has been enriched for the purpose. Specific developments (consideration of azeotropic mixturesc, solvent management, etc.) were necessary to overcome limitations that emerged during the work. In the short term, the goal is to exploit these new developments in order to optimize configurations and thereby improve industrial unit performance for renewable fuel production (production of aviation fuel via the alcohol-to-jet or e-Fuel process).
a- Correlation-type mathematical model in which the available data are used to estimate parameter values.
b- Gasoline production from naphtha.
c- Liquid mixture that has a constant boiling point while retaining a fixed composition.
References:
-
L. Mencarelli, Q. Chen, A. Pagot, and I.E. Grossmann. A Review on Superstructure Optimization Approaches in Process System Engineering. Computers & Chemical Engineering, 136, 2020.
>> https://doi.org/10.1016/j.compchemeng.2020.106808
-
L. Mencarelli, A. Pagot, and P. Duchêne. Surrogate-based Modeling Techniques with Application to Catalytic Reforming and Isomerization Processes. Computers & Chemical Engineering, 135, 2020.
>> https://doi.org/10.1016/j.compchemeng.2020.106772
-
P. Duchêne, L. Mencarelli, and A. Pagot. Optimization Approaches to the Integrated System of Catalytic Reforming and Isomerization Processes in Petroleum Refinery. Computers & Chemical Engineering, 141, 2020.
>> https://doi.org/10.1016/j.compchemeng.2020.107009
Scientific contact: alexandre.pagot@ifpen.fr