Metal- and ceramic-based solid foams are porous structures that have begun to be used relatively recently in the field of chemical processes although they have been the focus of research at IFPEN for a few years already.
Due to their 3D texture, made up of a multitude of juxtaposed spherical cavities (familiar in the field of heterogeneous catalysis), these structures are highly porous (around 70-80%) and have a large specific surface area. On the face of it, this is associated with good external transfer performances, in terms of both heat and matter. Therefore, they seemed to be suitable for rapid, highly exothermic chemical reactions, such as selective hydrogenations or methane oxidation reactions. This was thus the focus of specific research conducted in partnership with the Polytechnic University of Turin [1], which characterized matter transfer in open cell foams (OCFs).
The use of OCFs was subsequently considered for particle trapping at the top of hydrotreatment reactors for non-conventional feedstocks (vegetable oils, recycled plastics) and was the subject of PhD researcha carried out in partnership with the same university. The filtration mechanism inside foam pebbles was simulated via the Euler-Lagrange CFD method, using OpenFoam® and Ansys Fluent codes (Figure 1 left) [2], making it possible to precisely determine which morphological foam descriptors impact filtration efficiency.
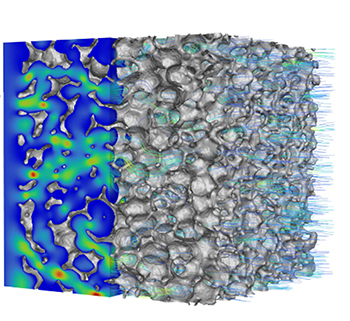
In parallel, capture tests were conducted using a dedicated experimental set-up, in order to quantify filtration efficiency (characteristic filtration height) in representative gas-liquid hydrodynamic conditions on vrac-packing of foam pieces.
Numerous analyses were also conducted by X-ray tomographyb to characterize the fouling by measuring the rate of cell plugging in waste foams, recovered from industrial reactors (figure 2).
In parallel, experiments of fouling were conducted at the laboratory,involving a fluid containing iron particles flowing through foam pieces.
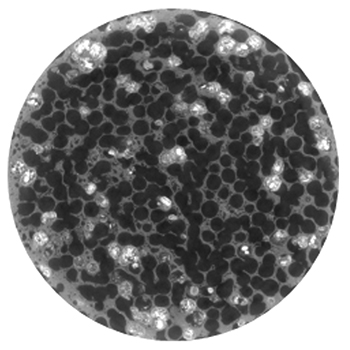
The results of capture and foam fouling experiments were modeled and integrated in a macroscopic 1D simulator to predict capture performances applicable to industrial catalytic reactors. This global capture model was successfully validated, through comparisons with cold-model experiments and data and matter analyses from industrial units.
All of the work carried out at IFPEN on ceramic or metallic foams has demonstrated the value of these structures both as catalytic supports with high transfer performances and for very high-capacity capture. The expertise acquired in the course of this research paves the way for the intensification of certain rapid reactions, and also for innovation in the field of filtration materials (OCF) with optimized geometries.
a- Thesis by Enrico Agostini, Fluid dynamics and mass transfer in porous media: Modelling fluid flow and filtration inside open-cell foams, 2023.
b- In partnership with IFPEN’s Physics and Analysis Division
References:
-
Carmen W. Moncada Quinter, Hernan G. Mazzei, Marion Servel, Frédéric Augier, Yacine Haroun, Jean-François Joly, Stefania Specchia, Investigating mass transfer coefficients in lean methane combustion reaction through the morphological and geometric analysis of structured open cell foam catalysts, Chemical Engineering Science, Volume 281, 5 November 2023, 119138.
>> https://doi.org/10.1016/j.ces.2023.119138
-
Enrico Agostini, Gianluca Boccardo, Daniele Marchisio, An open-source workflow for open-cell foams modelling: Geometry generation and CFD simulations for momentum and mass transport, Chemical Engineering Science, Volume 255, 29 June 2022, 117583.
>> https://doi.org/10.1016/j.ces.2022.117583
Scientific contact: Frédéric Augier