21.08.2024
4 minutes of reading
Geothermal fluids can be highly damaging even for supposedly resistant metal alloys. Whether it involves uniform corrosion or stress corrosion cracking, the phenomenon can be even more severe in the event of mineral deposit formation, which has the added disadvantage of reducing the thermal efficiency of the equipment affected. In order to gain a better understanding of these risks, research teams from IFPEN, INSA-Lyon, Mines de Saint-Etienne and the French Corrosion Institute have joined forces to conduct the GeoSteelCor project. Methodologies have been developed to control mineral deposit formation on metallic surfaces, in laboratory conditions, as well as more realistically in a high-pressure and high-temperature corrosion test loop. These methodologies have also been used to study the impact of mineral deposits on stress corrosion cracking.
Highly corrosive geothermal waters
The transition towards a low-carbon economy requires to intensify the use of more sustainable energy sources, such as geothermal energy. Highly mineralized geothermal waters, and the associated sour gases (CO2, H2S) can be sources of corrosion affecting the equipment employed, particularly if the equipment is made of carbon steel. For some extremely corrosive conditions, grades of stainless steel or indeed nickel alloys may be necessary. In this case, a stress corrosion cracking-type degradation mode needs to be considered. In addition, these corrosion phenomena can be exacerbated by the presence of mineral deposits that readily form in these very ion-rich solutions, during changes of environmental conditions (temperature and/or pressure variation) impacting the fluids. It should also be noted that this clogging leads to losses of thermal efficiency and plugging risks.
A coordinated action plan to study the impact of mineral deposits
In order to gain a better understanding of the influence of mineral deposits on the risks of corrosion and stress corrosion cracking of steels, specialized teams from IFPEN, INSA-Lyon, Saint-Etienne École des Mines, and the French Corrosion Institute joined forces to conduct research, in particular within the framework of the GeoSteelCor project1. The research was aimed at developing methodologies to control mineral deposit formation on metallic surfaces, initially in simple laboratory conditions, and then scaled up to a high-pressure and high-temperature corrosion test loop. These methodologies were also used to study the impact of mineral deposits on stress corrosion cracking.
1 Project financed by the French National Research Agency (ANR 21-CE05-0024)
Monitoring of the electrochemical response of a metal surface during mineral deposit formation
In practice, mineral deposit precipitation in industrial installations often occurs on surfaces exposed to heat exchange. That is because the solubility in water of numerous mineral species varies with temperature. This property was used to develop an original experimental set-up in which the outer surface of a steel tube is exposed to a highly mineralized corrosive environment, while a heat-carrying fluid circulates inside it [1-3]. Heat exchanges through the walls promote surface precipitation, and it is possible to conduct electrochemical measurements to monitor the evolution of the metal’s response during deposit formation (Figure 1).
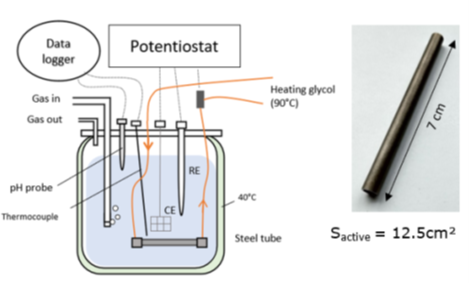
Mixed deposits several hundred micrometers thick containing two polymorphs of calcium carbonate (aragonite and calcite) formed within a few days (Figure 2).
![]() |
To explain the effect of this deposit on corrosion, an electrochemical model involving a diffusional limitation associated with porous electrode behavior was proposed (Figure 3).
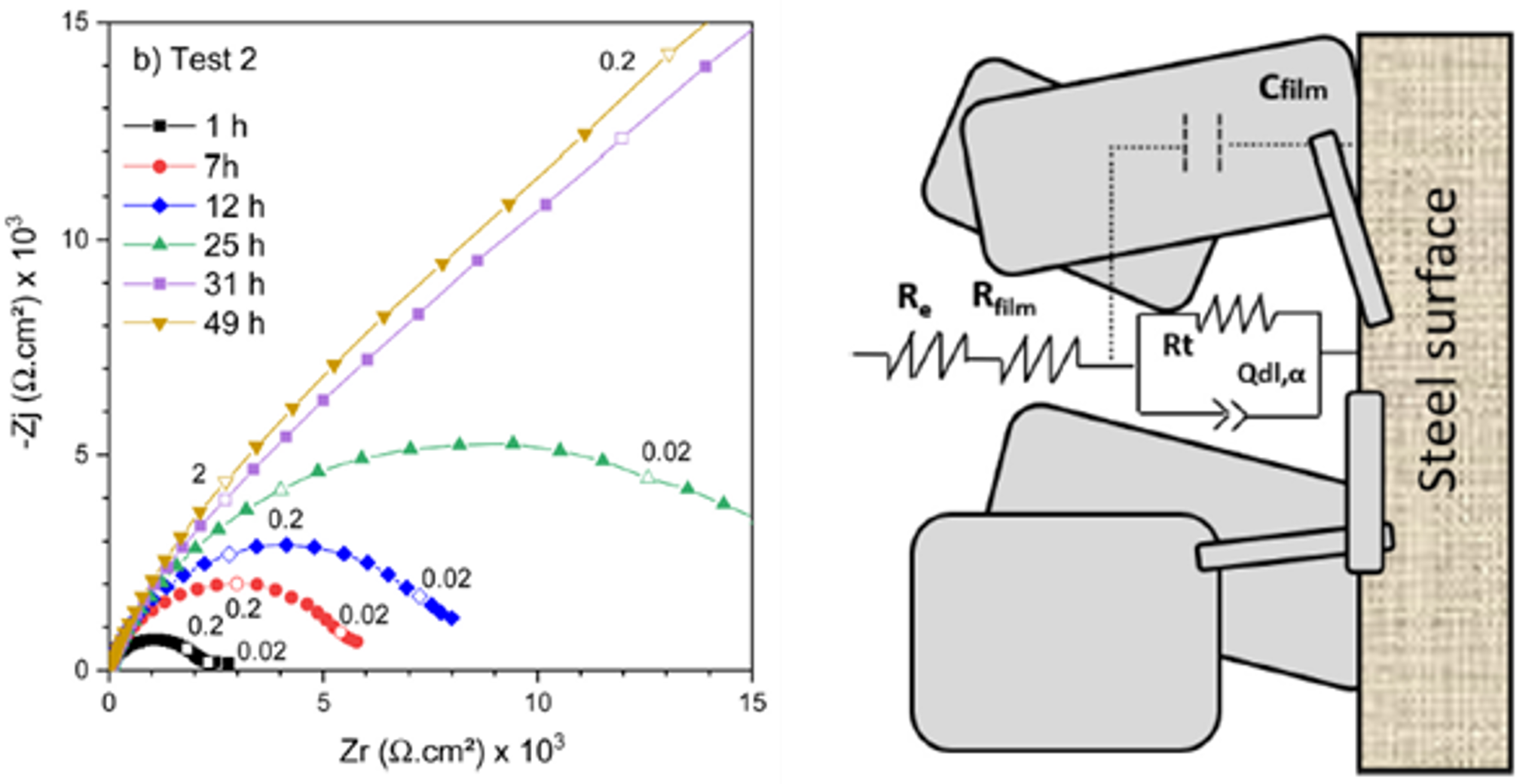
Coupling mechanical stresses, mineral deposits and corrosive environments
In order to study the impact of mineral deposits on the risks of stress corrosion cracking, a new set-up was developed to promote deposit formation on tensile specimens (Figure 4). The latter was placed in an aqueous solution with a pH close to neutral (favorable to calcium carbonate deposit formation at ambient temperature and pressure) and then heated to 90°C thanks to an inside heated circulating fluid. No effect of the deposit on stress corrosion cracking resistance was observed [2, 4].
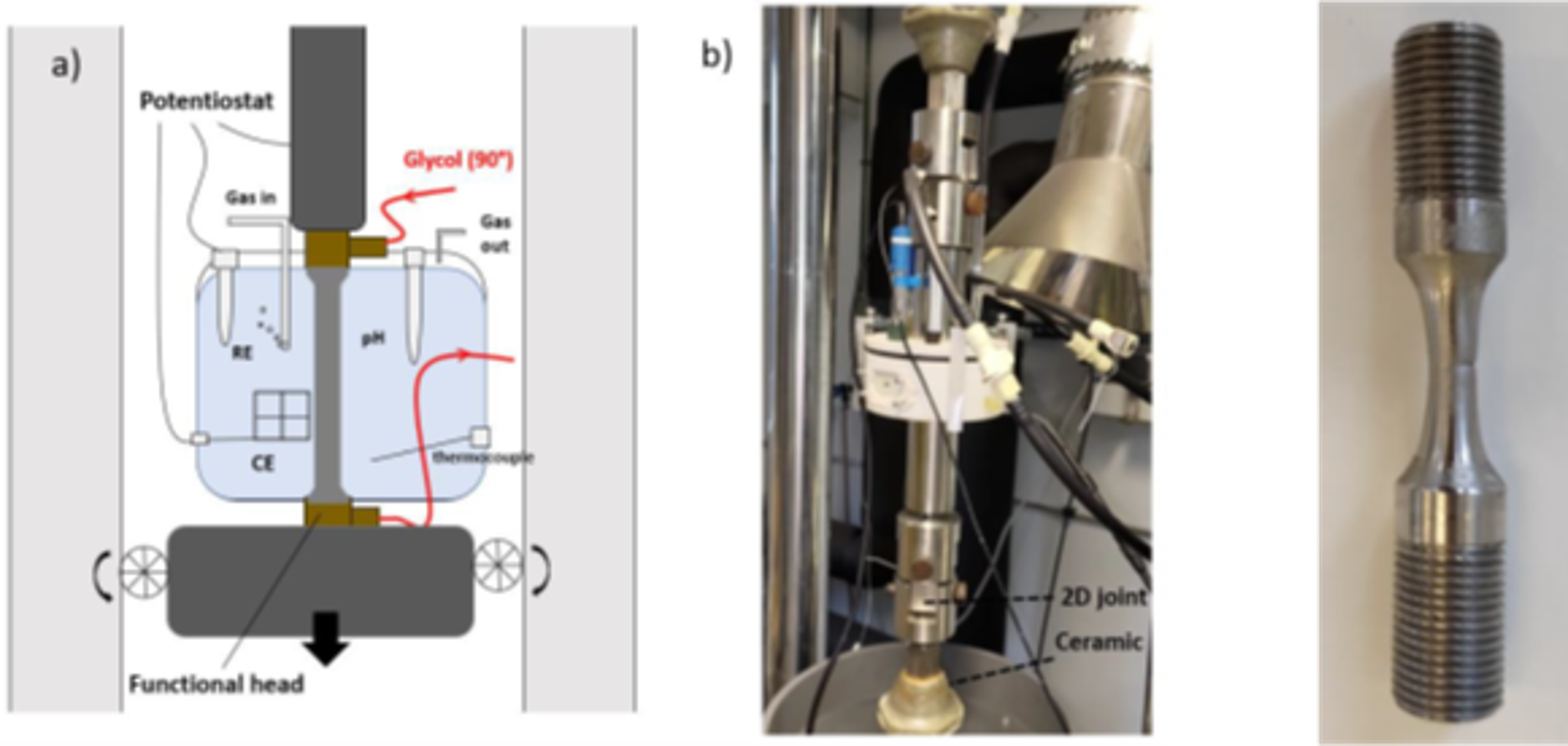
Scale change and transfer of methods to a HP-HT corrosion test loop
Industrial geothermal installations are very often exposed to fluids at temperatures well in excess of 100°C and under pressures of several bar or tens of bar. In order to gain a better understanding of corrosion risks and the effects of deposits in environments representative of these conditions, the methodologies described above were transferred to a corrosion test loop able to operate at pressures of up to 300 bar and a maximum temperature of 200°C (figure 5) [5].
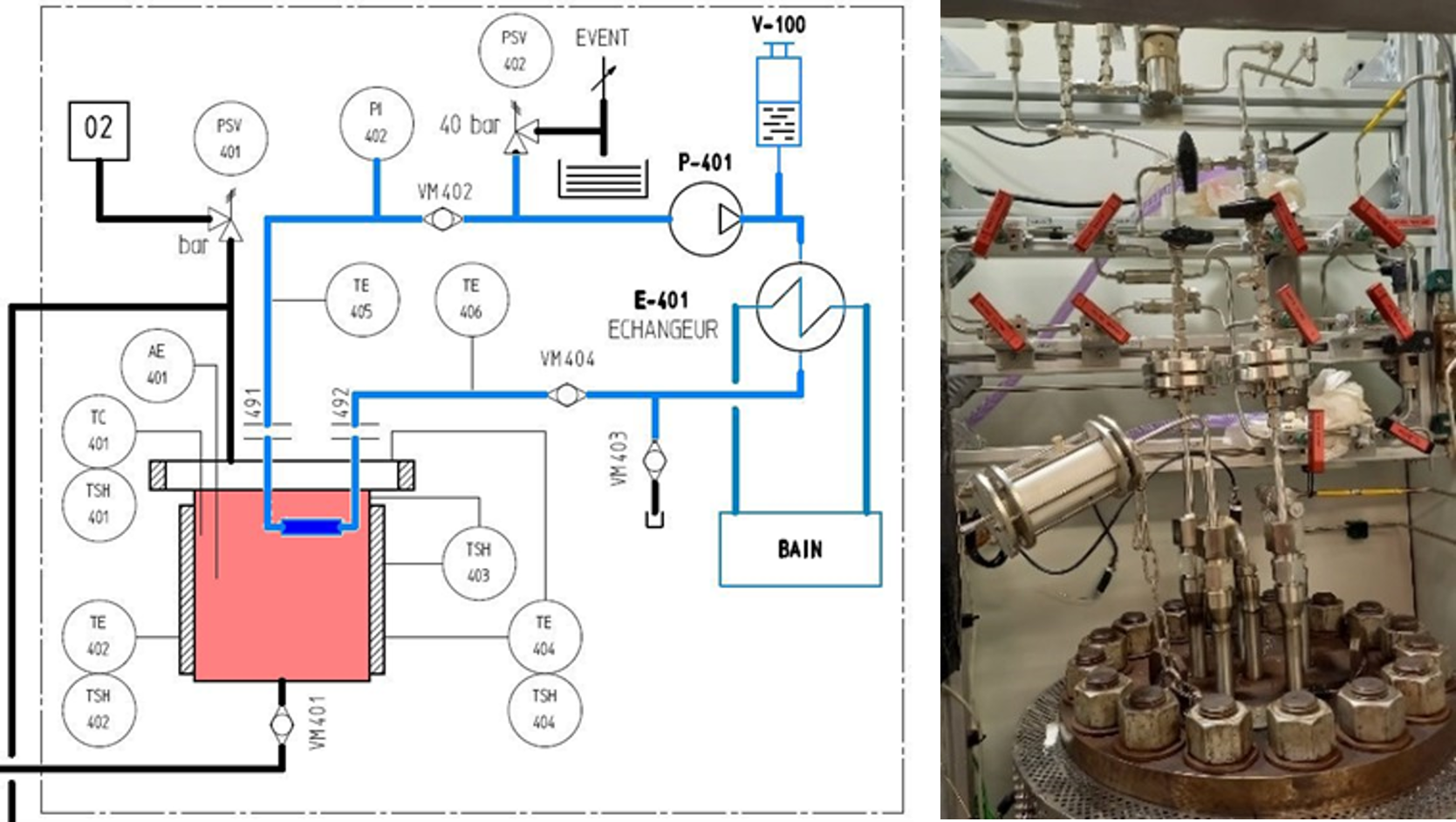
Conclusion: knowledge and procedures that address industry’s challenges
This collaborative fundamental research provides a better understanding of the effect of mineral deposits on corrosion and stress corrosion cracking in steels. The original methodology developed to induce mineral deposits in a controlled manner on metal surfaces has the advantage of being both easy to implement and close to the actual industrial conditions encountered in heat exchangers. It enables electrochemical monitoring of the response of the metal surface during deposit formation, and can also be coupled with mechanical stresses.
On the basis of laboratory tests, an electrochemical model was developed to describe carbon steel behavior during the formation of such deposits down to thicknesses measured in millimeters.
These developments, combining deposit formation and mechanical stresses, were then transferred to a high-pressure/high-temperature corrosion test loop, allowing tests to be carried out under conditions more representative of geothermal energy production. These new methods, and the knowledge they have generated, are now being used to optimize material selection and mineral deposit control strategies in different industrial environments.
References :
[1] G. Aristia et al., Méthodologies pour l’étude de l’impact des dépôts minéraux sur la corrosion des matériaux métalliques dans des eaux géothermiques artificielles, Congrès Matériaux 2022, Colloque 14 ID 82075, Lille (2022)
[2] F. Bertin et al., Electrochemical impedance response of a thick and porous calcium carbonate layer deposited by thermal growth on a carbon steel electrode, Corrosion Science 227 (2024) 111778
>> DOI: doi.org/10.1016/j.corsci.2023.111778
[3] F. Bertin, Impact of mineral scaling on corrosion and stress corrosion cracking of steels in geothermal environment, PhD thesis, Ecole des Mines de Saint-Etienne (2024)
[4] F. Bertin et al., Evaluation of surface corrosion and stress corrosion cracking of 13Cr stainless steel in presence of calcium carbonate scales in simulated geothermal environment containing CO2, 74th annual meeting of the International Society of Electrochemistry, Lyon (2023)
[5] G. Artisia et al., Methodologies to evaluate corrosion of carbon and stainless steels in artifical geothermal solutions, AMPP 2024 annual conference, New-Orleans (2024)
Scientific contacts: François Ropital, gaurav.joshi@ifpen.fr, françois grosjean@ifpen.fr, Jean Kittel
Most of the research presented was conducted within the framework of the PhD thesis by Federico Bertin “Impact of mineral deposits on the risk of stress corrosion of steels under geothermal conditions containing CO2 “ as well as within the framework of the ANR 21-CE05-0024 GeoSteelCor project conducted in partnership with INSA Lyon, Ecole des Mines de Saint-Etienne and the French Corrosion Institute. We extend our sincerest thanks to them.
You may also be interested in
Understanding the causes of corrosion through molecular modelling - Application to stainless steels in CO2 environments -
Carbon steel in self-defense mode against corrosion
Carbon or low-alloy steel corrosion, by aqueous media containing CO2, hampers the development of numerous technologiesa f