04.07.2024
4 minutes of reading
Carbon steel is a construction material that is widely used in industry, due to its excellent cost/performance ratio. Nevertheless, in certain applications, it can come into contact with an aggressive environment, such as aqueous environments that have been acidified by the presence of CO2, leading to corrosion-induced deterioration. In order to gain a better understanding and improve the protection of carbon steels in environments of this type, corrosion teams from IFPEN, INSA-Lyon’s Mateis Laboratory and the University of Leeds’ Institute of Functional Surfaces (IFS) have pooled their expertise to conduct joint research. The research is aimed at controlling the performance of the “pseudo passive” surfaces observed on these steels, developing characterization methodologies to study the protection mechanisms involved.
Corrosion resistance, an Achilles’ heel for different usages related to the ecological transition
The transition to a low-carbon economy requires new technologies. Some of these, including CCUS (Carbon Capture Utilization and Storage) and biofuel synthesis, involve aqueous effluents containing CO2 in solution. These environments may be a source of corrosion affecting the equipment employed, particularly if it is made of carbon steel. Carbon steel is associated with numerous advantages due to its low cost, availability, and recyclability, as well as its mechanical and assembly (machining, welding) properties. However, its corrosion resistance remains a weak point. Nevertheless, in certain conditions, its surface may be protected by the formation of a “pseudo passive” layer. A layer of iron oxide or carbonate is formed on the surface, which can potentially be reinforced by the incorporation of other metallic elements.
Evaluation of the physicochemical conditions close to the corroding surface
In order to better characterize the aqueous environment in the corrosion zone, a specific set-up (figure 1) was developed to evaluate the local pH in the closed vicinity of a sample immersed in an aqueous medium containing CO2. The set-up takes the form of a carbon steel grid.
![]()
|
![]()
|
As indicated in figure 2, at the interface where corrosion takes place, the pH measured is less acidic by around 0.4 units of pH compared to the pH of the solution a long way from the interface [1]. This local condition is favorable to the formation of a pseudo passive layer.
Carbon steel “pseudo passivity” protection mechanisms
Electrochemical measurements have confirmed that the pseudo-passive state is characterized by a change in open circuit potential and a significant reduction in the corrosion rate. This can be observed in figure 3 with, after 10 days, a corrosion rate that has become so low (less than 0.02 mm/year) that it enables long-term use of carbon steel.
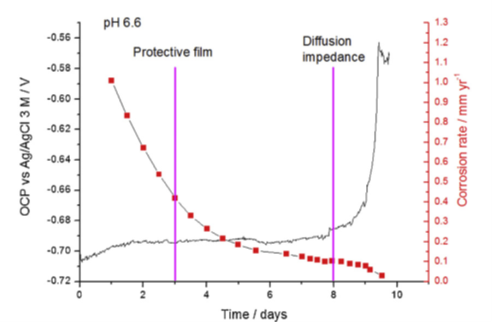
For a sample exposed to 80°C and a pH of 6.6, surface analyses identified traces of a magnetite phase (Fe3O4) at certain places, beneath a more dominant iron carbonate (FeCO3) film (figure 4). In addition, over the course of time, the corrosion layer acquires a very low porosity, resulting in the formation of a “diffusion barrier”. This is indicated in figure 3 by a significant increase in the open circuit potential (OCP), which is considered to be a key corrosion protection indicator [2].
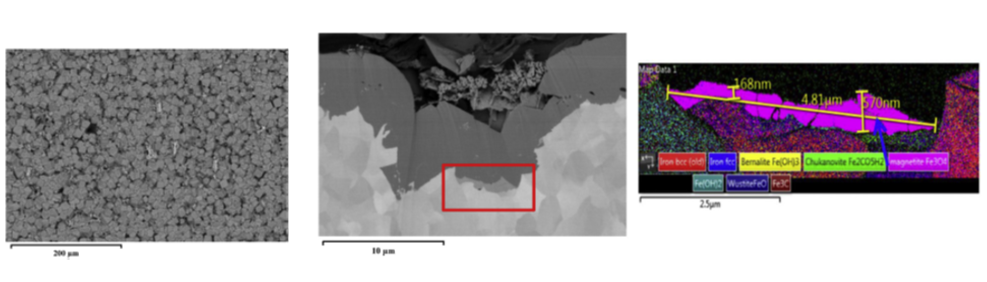
1 Electron Backscatter Diffraction
In situ corrosion monitoring using synchrotron radiation
In situ synchrotron X-ray diffraction (SR-XRD) was also used to monitor the evolution of corrosion products on X65 carbon steel in an aqueous environment containing CO2 (following exposure to 80°C, pH 6.3–7.3). A custom-designed flow cell was built for the purpose, enabling real-time monitoring of concomitant changes in electrochemical behavior and corrosion product growth [3]. Measurements were carried out both during natural "pseudo-passivation" stages and under potentiodynamic polarization conditions , to investigate electrochemical mechanisms in the cathodic and anodic domains (Figure 5).
2 i.e., varying the sample potential
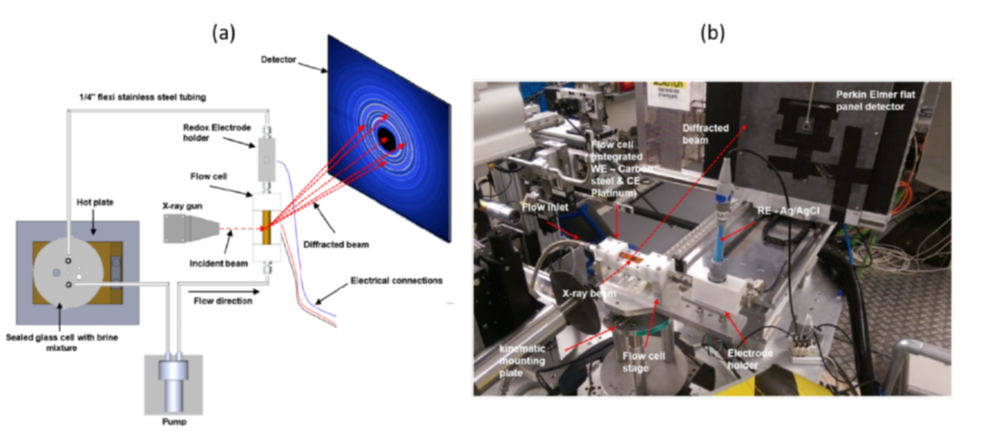
The protectivity (reflected by a nobler open circuit potential) observed during ”pseudo-passivation” is strongly linked to the accumulation of iron carbonate (FeCO3) on the steel surface (figure 6). The chukanovite Fe2(OH)2CO3 was only detected at higher anodic potentials (associated with a rapid steel dissolution rate), outside the pseudo passive protection domain (figure 7): this phase thus appears to be associated with the active dissolution of carbon steel [3].
![]()
|
![]()
|
Conclusion
This collaborative fundamental research led to a better understanding of the protection mechanisms association with the “pseudo passivation” of carbon steel in aqueous environments containing carbon dioxide. It also demonstrates the interest of the methodologies implemented, in particular in situ electrochemistry in a synchrotron. These methodologies were also used to study the reinforcement of protection by the incorporation of magnetite in the pseudo passive layer [4-5], as well as the impact of contaminants, such as oxygen, on the duration of pseudo passivation. [6-7]
References:
[1] R. de Motte, R. Mingant, J. Kittel, F. Ropital, P. Combrade, S. Necib, V. Deydier, D. Crusset, Near Surface pH Measurements in Aqueous CO2 Corrosion, Electrochemica Acta, 2018, 290, 605-615
>> DOI : https://doi.org/10.1016/j.electacta.2018.09.117
[2] R.de Motte, E. Basilico, R. Mingant , J. Kittel, F. Ropital, P. Combrade, , S. Neicib,, V. Deydier, D. Crusset,, S. Marcelin, A study by electrochemical impedance spectroscopy and surface analysis of corrosion product layers formed during CO2 corrosion of low alloy steel, Corrosion Science, 2020, Volume 172 1 August Article 108666
>> DOI : https://doi.org/10.1016/j.corsci.2020.108666
[3] J. Owen; D. Burkle, E. Basilico, S. Marcelin, F. Ropital; G.R. Joshi; J. Kittel; A. Kleppe, R.C. Woollam, R. Barker, In situ SR-XRD analysis of corrosion product formation during ‘pseudo-passivation’ of carbon steel in CO2-containing aqueous environments, Corrosion Science, 225 (2023) 111598,
>> DOI : https://doi.org/10.1016/j.corsci.2023.111598
[4] J. Owen, R. Barker, F. Ropital, G. R. Joshi, J. Kittel, R. Jacklin, D. Burkle, E. Straume, S. N. Karlsdóttir, Modified magnetite surface layers on carbon steel in aqueous CO2 environments, NACE/AMPP 2023 Conference paper 19127
[5] J. Owen; F. Ropital; G.R. Joshi; J. Kittel; R. Barker, Galvanic effects induced by siderite and cementite surface layers on carbon steel in aqueous CO2 environments, Corrosion Science, 2022-10,
>> DOI : https://doi.org/10.1016/j.corsci.2022.110762
[6] E. Basilico, S. Marcelin, R. Mingant , J. Kittel, M. Fregonese, J. Owens, R. Barker, A. Neville, F. Ropital, Effect of O2 contamination on carbon steel pseudo-passive scales in CO2 aqueous solutions, Corrosion Science, 2022, Vol 205, Article 110388
>> DOI : https://doi.org/10.1016/j.corsci.2022.110388
[7] E. Basilico, S. Marcelin, R. Mingant , J. Kittel, M. Fregonese, F. Ropital, The effect of chemical species on the electrochemical reactions and corrosion product layer of carbon steel in CO2 aqueous environment: A review, Materials and Corrosion, 2021, 1, 16
>> DOI : https://doi.org/10.1002/maco.202012118
Scientific contacts: François Ropital, Jean Kittel, gaurav.joshi@ifpen.fr
The research presented was primarily conducted within the framework of the post-doctoral research by Rehan de Motte, the PhD thesis of Edoardo Basilico and the scientific visit at IFPEN of Joshua Owens. We extend our sincerest thanks to them.
You may also be interested in
Carbon steel in self-defense mode against corrosion
Carbon or low-alloy steel corrosion, by aqueous media containing CO2, hampers the development of numerous technologiesa f
The French Corrosion Institute and IFPEN sign a framework partnership agreement relating to the energy transition
Self-repair against localized corrosion
Due to their low cost and their good mechanical properties, carbon steels are a widely used material, including for equipments in contact with harsh environments, such as aqueous media containing CO2...