02.12.2018
5 minutes of reading
Zeolites are crystalline aluminosilicates that can be used for the manufacture of catalysts thanks to their physical and chemical properties and, in particular, their organized and regular microporous network, within which some of the catalytic reactions take place.
The accessibility of active sites within the zeolite crystals is a crucial parameter for ensuring effective catalyst function; thus the easy diffusion of reactants and products in their pores is a major challenge for industrial players for the design of these products.
The Y zeolite and Beta zeolite are amongst the most widely used solids for manufacturing catalysts employed for hydrocarbon conversion. These entirely microporous materials are simple and inexpensive to prepare, but traditional syntheses only make it possible to obtain crystals of relatively large dimensions (in the region of a micrometer, figure 1a). These "large" crystals are associated with significant limitations in terms of the accessibility of hydrocarbon molecules within zeolites. This means that the latter are under-exploited and, in order to address this, different strategies exist in the literature, all aimed at reducing these constraints on the transport of molecules within the material, by reducing theirresidence time. The destructive approach (top-down) consists in "digging holes" in large-sized crystals (figure 1c); conversely, the constructive approach (bottom-up) is aimed at assembling crystals of smaller dimensions, known as nanocrystals, thereby creating hierarchized porosity (figure 1b).
A third, recently emerged option is the preparation of hollow zeolite crystals [1]. These solids are presented either in the form of a specific assembly of nanocrystals (figure 1d), or in the form of micrometric crystals containing a single central cavity (figure 1e). The thickness of the shell can be reduced to a few tens of nanometers while keeping unchanged the external surface of the crystals. The other benefit of such morphologies is that they can encapsulate metal particles that can only be accessed by molecules of a smaller diameter than the diameter of the micropores of the zeolite shell, leading to a direct impact on reaction selectivity (figure 1f).
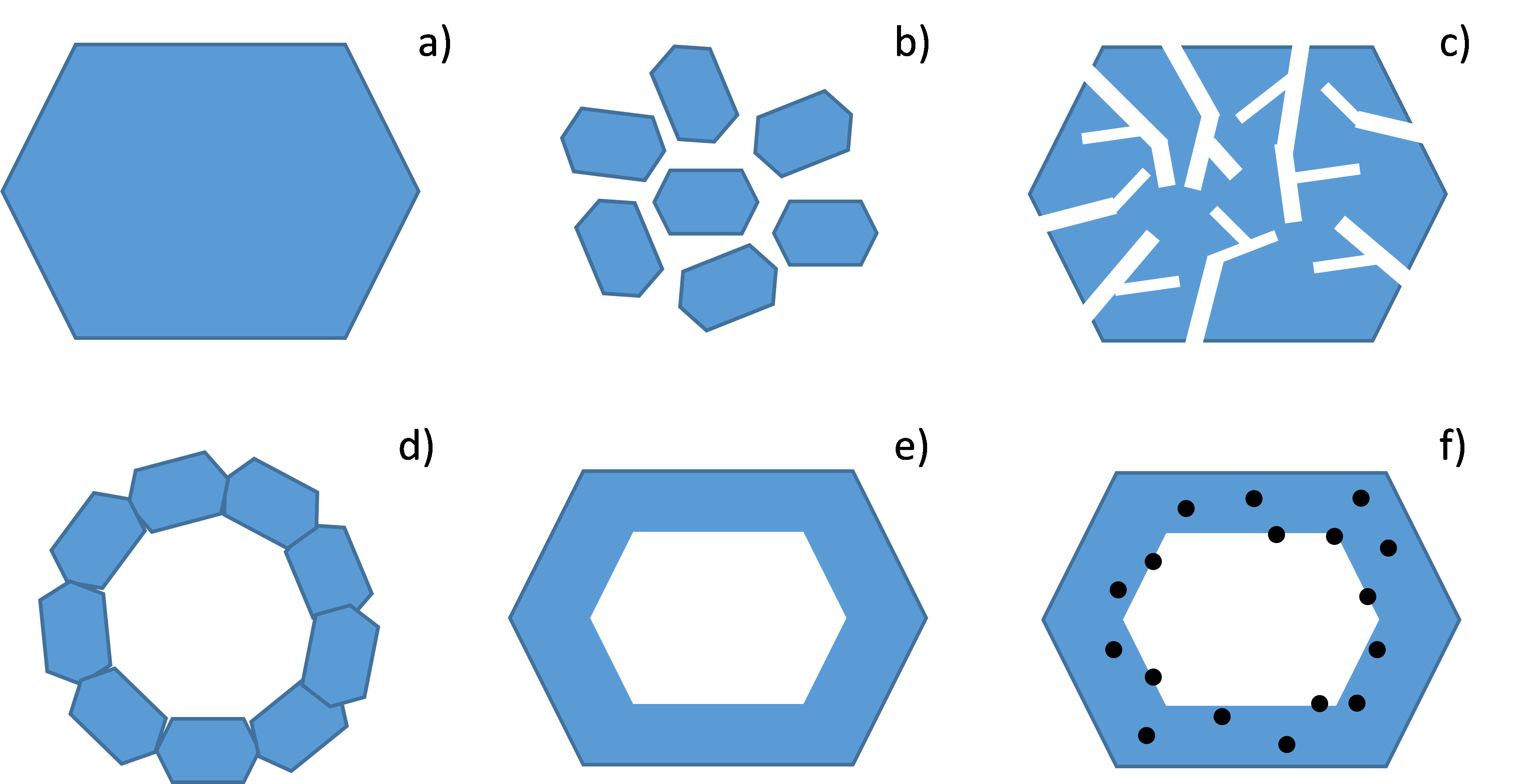
IRCELyon and IFPEN are currently working together within the framework of two PhD theses dedicated to the preparation of new materials of this type: zeolite nanocapsules and nanoboxes.
In the first thesis [2] they successfully obtained hollow, highly crystallized Y zeolites via the post-synthesis modification, in three steps, of conventional Y zeolite crystals (figure 2):
- micrometric crystals were initially dealuminated via the circulation of silicon tetrachloride gas;
- they were then treated with an acid solution to eliminate aluminum debris, thereby generating a silicon-rich center;
- a basic treatment step in the presence of a protective aluminum source then made it possible to preferentially dissolve the silicon core of the crystals.
The internal cavity of the resulting hollow zeolites has a diameter of around 0.8 µm and it is surrounded by 0.12 µm-walls (figure 3). These structures are more stable and harbor fewer defects than other materials referenced in the literature. After impregnation by a platinum salt, followed by a reduction operation, a highly selective bi-functional catalyst was obtained due to the fact that all of the platinum nanoparticles are located within the zeolite wall [3].
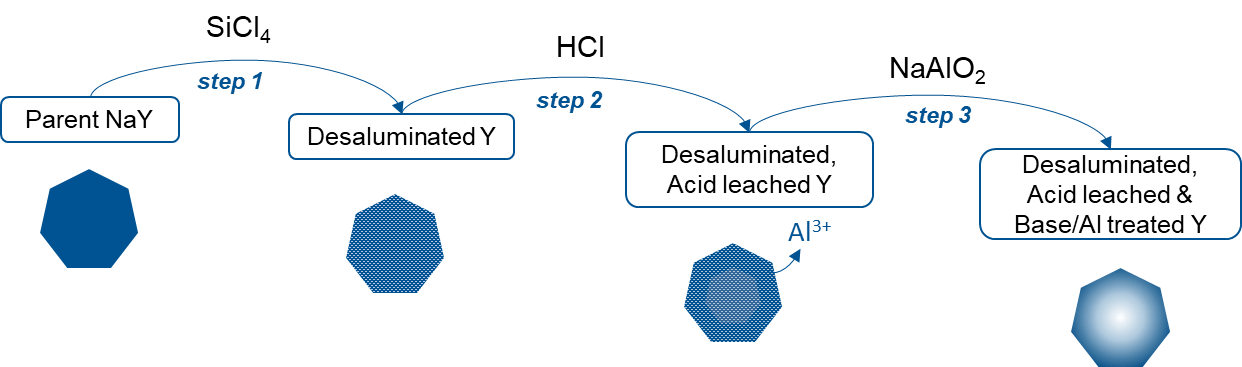
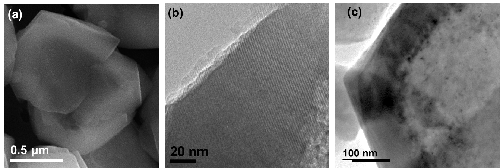
Dans la seconde thèse[4], des cristaux creux de zéolithe Beta ont été obtenus par une méthode différente, utilisant la dissolution-recristallisation (figure 4) :
- une zéolithe zincosilicique (CIT-6) de structure analogue à la zéolithe aluminosilicique Beta a d'abord été préparée par synthèse hydrothermale ;
- les cristaux formés ont ensuite été mis en présence d'un gel aluminosilicaté, à une température de 150 °C, entraînant une cristallisation de zéolithe Beta à la surface de la CIT-6, accompagnée d'une dissolution de cette dernière.
At the end of the process, the material obtained takes the form of a beta zeolite crystal with an internal cavity corresponding to the dissolved CIT-6 particle. The addition of a platinum precursor directly before the transformation step makes it possible to add nanoparticles of this metal inside the Beta capsule (figures 4 and 5).
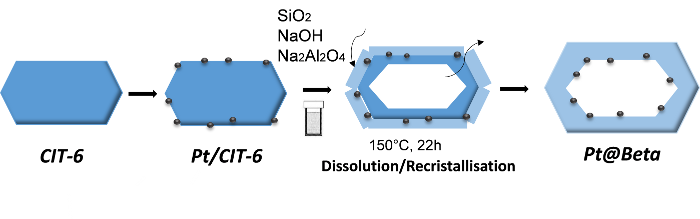
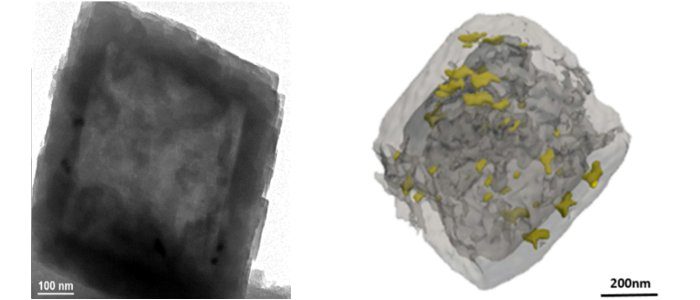
These two new types of hollow materials obtained using these original approaches are undergoing catalytic evaluation [a] in order to quantify the gains in terms of activity and/or selectivity provided by these unusual morphologies. Their global diffusion properties are also being characterized using transitional adsorption techniques (ZLC[b], TAP[c]). Finally, the impact of improved diffusion in this type of morphology is being analyzed [5] based on the relationship between the effectiveness factor[d] and the Thiele modulus[e], which is directly related to the characteristic lengths of catalyst particles.
[a] hydroisomerization tests on a model molecule (n-hexadecane) at IFPEN and cyclohexene hydrogenation tests at IRCELyon
[b] Zero Length Column
[c] Temporal Analysis of Products
[d] quantity representing the degree of use of a catalyst grain (effective volume), expressed by the relationship between the actual observed reaction speed and the intrinsic chemical reaction speed
[e] a dimensionless number, used in chemical kinetics to characterize the limiting factor of a heterogeneous catalytic reaction with a porous catalyst; it expresses the relationship between the intrinsic reaction speed on a catalyst and the flow of reactants via diffusion towards this catalyst
Publications
[1] C. Pagis, A.R. Morgado Prates, D. Farrusseng, N. Bats, A. Tuel, Hollow Zeolite Structures: An Overview of Synthesis Methods, Chem. Mater. 28 (2016) 5205-5223
>> DOI : 10.1021/acs.chemmater.6b02172
[2] C. Pagis, A.R. Morgado Prates, N. Bats, A. Tuel, D. Farrusseng, High-silica hollow Y zeolite by selective desilication of dealuminated NaY crystals in the presence of protective Al species, Cryst. Eng. Comm. 20 (2018) 1564-1572
>> DOI : 10.1039/C8CE00121A
[3] C. Pagis, C. Bouchy, M. Dodin, R. Martinez Franco, D. Farrusseng, A. Tuel, Oil Gas Sci. Technol. - (publication soumise)
[4] A.R. Morgado Prates, C. Pagis, F.C. Meunier, L. Burel, T. Epicier, L. Roiban, S. Koneti, N. Bats, D. Farrusseng, A. Tuel, Hollow Beta Zeolite Single Crystals for the Design of Selective Catalysts, Cryst. Growth Des. 18 (2018) 592-596
>> DOI : 10.1021/acs.cgd.7b01635
[5] C. Pagis, F. Meunier, Y. Schuurman, A. Tuel, M. Dodin, R. Martinez Franco, D. Farrusseng,ChemCatChem 10 (2018) - (sous presse)