28.03.2023
3 minutes of reading
For transport segments where electrification is complex, such as heavy-duty vehicles (long-haul trucks and off-road1 vehicles ), hydrogen mobility appears to be a promising alternative to address the challenges of reducing the carbon footprint of the transport sector as a whole.
While fuel cells have been the focus of a substantial amount of research in the context of low-carbon mobility, the IC engine using hydrogen as a fuel appears to be equally feasible as an alternative in order to significantly reduce CO2 and pollutant emissions.
This has been demonstrated by research conducted by IFPEN, FEV and Aachen University as part of the European LONGRUN project.
To use hydrogen as a fuel, the main challenge is to ensure a high level of efficiency while controlling NOx emissions and abnormal combustion. In order to identify the optimization levers for this energy conversion system and gain a better understanding of the phenomena at play, IFPEN partnered up with FEV and Aachen University to conduct an experimental and numerical study [1] within the framework of the European LONGRUN project.
Validation of a 3D approach dedicated to the hydrogen engine
IFPEN’s expertise in the field of reactive CFD2 modeling and simulation was employed to formulate a first multi-physical 3D numerical approach to predict the behavior of an H2 engine.
The simulation is based on a RANS3 formalization, implemented in the CONVERGETM calculation code, and involves the combined use of several physical sub-models:
• The Extended Coherent Flame Model (ECFM) [2] which describes the propagation of a partially pre-mixed H2 flame;
• The Tabulated Kinetics of Ignition (TKI) model [3] for the prediction of phenomena related to self-ignition (pre-ignition and knocking);
• and the detailed post-flame chemical model (activated only in the burned gas zone) for the prediction of NOx emissions.
The modeling approach was validated using experimental measurements provided by FEV and Aachen University for a single-cylinder Diesel engine specifically converted to H2 for the LONGRUN project.
The validation of the numerical model was initially conducted on a homogeneous PFI4 configuration to avoid uncertainties associated with modeling the Air/H2 mixture in the combustion chamber.
Figure 1 details this validation, which related, in particular, to the prediction of flame propagation, abnormal combustion phenomena (knocking) and NOx emissions.
1 Off-road: Any type of vehicle capable of being driven on and off a paved or gravel surface
2 CFD: Computational Fluid Dynamics
3 RANS: Reynolds-Averaged Navier-Stokes
4 PFI: Port Fuel Injection
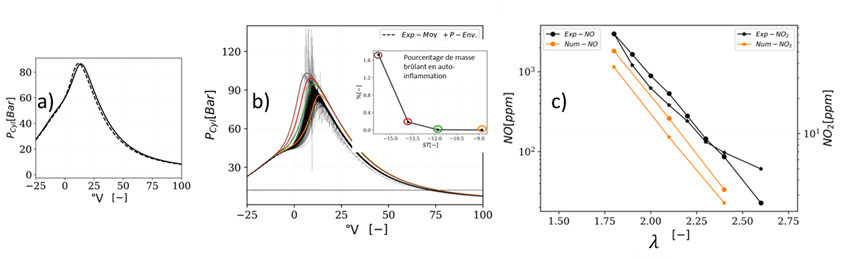
The CFD model previously validated for the PFI configuration was then used to simulate a configuration with direct H2 injection.
While reproducing the good evolution of cylinder pressure (and thus flame propagation) compared to measurements, the calculation made it possible to demonstrate that the optimization of mixture formation on a direct injection (DI) configuration is a key lever for improving engine efficiency and reducing NOx emissions.
Figure 2 shows that NO and NO2 formation is closely associated with the mixture preparation described by the variable λ5. Moreover, this first validation confirmed the relevance of 3D calculation as a tool to facilitate and support the design of future hydrogen powertrains.
5 Air/Fuel ratio
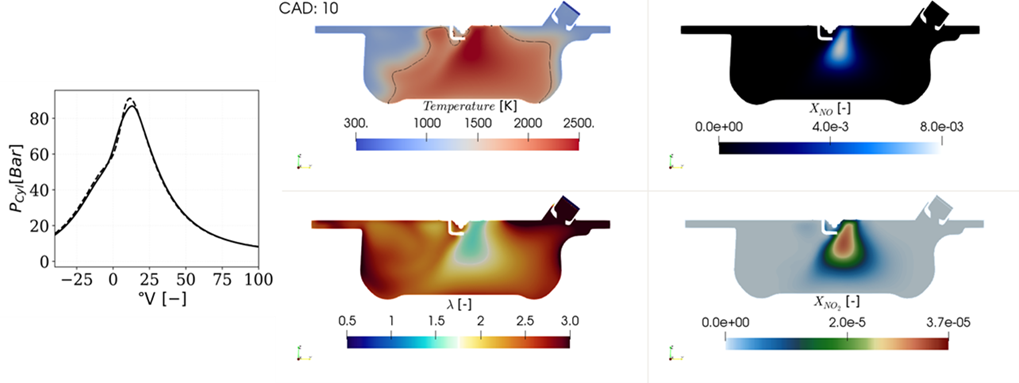
Ongoing research to improve the predictive capacity of 3D simulation
The promising results obtained during this research encourage further studies involving new simulation approaches in order to continue to improve the robustness and predictive capacity of calculations over a broader operating range (regime and load).
In particular, this research will consist in improving the modeling of the H2/air mixture in the combustion chamber during direct injection, as well as the description of flame propagation and the self-ignition phenomenon.
References
[1] Maio, G., Boberic, A., Giarracca, L., Aubagnac-Karkar, D., Colin, O., Duffour, F., ... & Pischinger, S. (2022). Experimental and numerical investigation of a direct injection spark ignition hydrogen engine for heavy-duty applications. International Journal of Hydrogen Energy, 47(67), 29069-29084.
[2] Colin, O., Benkenida, A., & Angelberger, C. (2003). 3D modeling of mixing, ignition and combustion phenomena in highly stratified gasoline engines. Oil & gas science and technology, 58(1), 47-62.
[3] Robert, A., Richard, S., Colin, O., Martinez, L., & De Francqueville, L. (2015). LES prediction and analysis of knocking combustion in a spark ignition engine. Proceedings of the Combustion Institute, 35(3), 2941-2948.
Scientific contact : olivier.laget@ifpen.fr
You may also be interested in
A better description of turbulent flows for hydrogen powertrains
Within the framework of a global policy to reduce the emissions produced by the transport sector - particularly road transport - IFPEN is focusing on a complementary option along with vehicle electrification: the use of hydrogen powertrains. However, the use of hydrogen in IC engines first requires a comprehensive understanding of different phenomena, associated, for example, with interactions between the fuel and air...